01
現場プロセス
現場プロセスのDXで、
業務改革・効率化を
製造業界では、複雑化・老朽化・ブラックボックス化したシステム群を卓越した経験とノウハウを保持した要員で運用していることが多く、これらシステム群が製造現場に残ることで、2025年以降、毎年最大12兆円の損失が発生すると言われています。さらに生産年齢人口の減少や、団塊世代の大量退職が引き起こす人手不足・技術の継承も大きな問題となっており、現場プロセスのDX化による業務改革・効率化が急務です。
Point of DX
現場プロセスのDXに
必要なこととは
01
まずは、
人やモノの「見える化」
DXの第一歩は、現場で何が起きているのかを把握することから。高精度な屋内測位システムを活用すれば、現場作業員や中間生産物、フォークリフトなどの所在や動きのデータを収集でき、人手を介さずリアルタイムに見える化できます。

02
データ収集と分析を
セットで考える
データは見える化・分析をしてはじめて意味を持ちます。データの品質・精度が分析に影響するため、分析内容を事前に設計することで、より効果的な結果を得られます。つまり、データ収集と分析は常にセットで考えることが大切なのです。
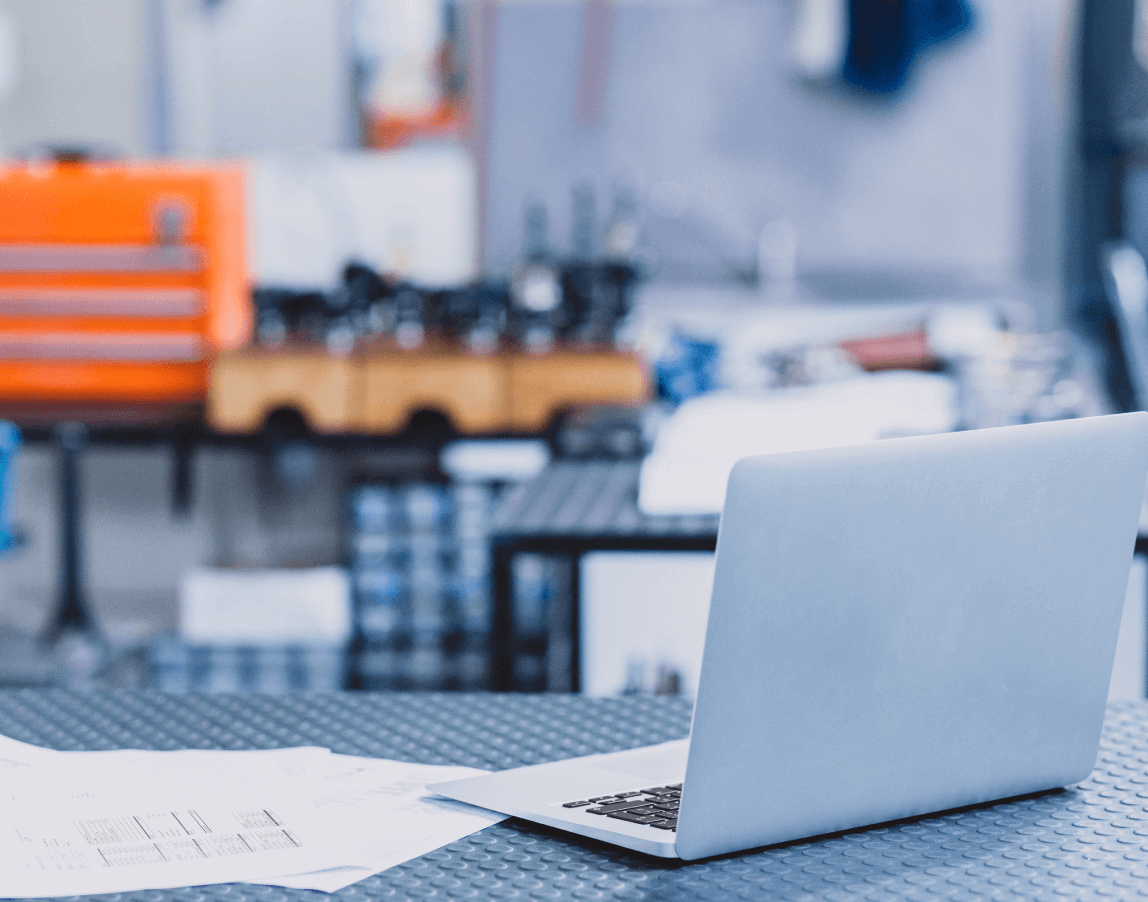
03
現場やシステムへのフィードバック
データ収集や分析で見えてきた課題に対し、部署の枠を超え全体を見通して最適なDXを計画・推進。実際に現場にシステムを導入・運用・検証し、さらにそこで得られた結果をまたフィードバックし、改善するサイクルを回すことが重要です。
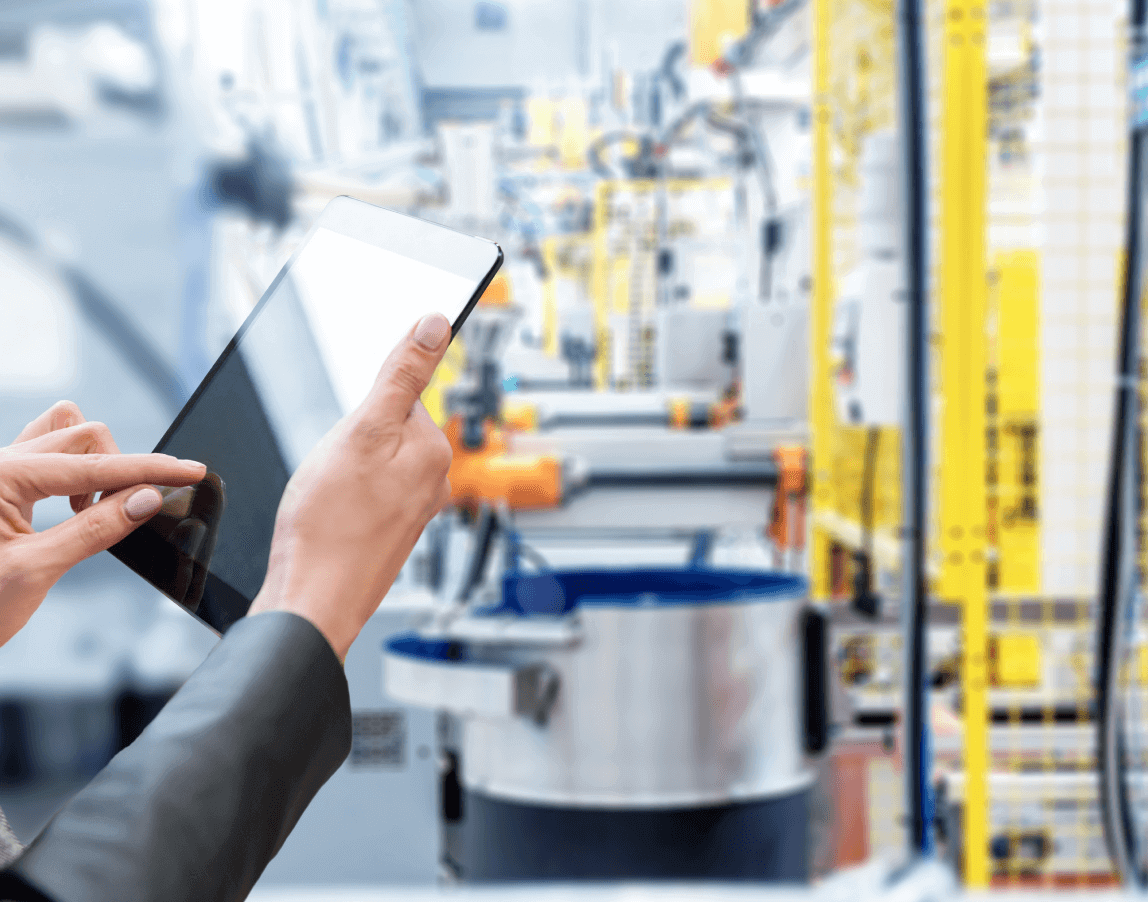
Point of Solution 現場プロセスのDXに必要なこととは
こんなお客様の悩みに...
人の手による作業・
工程管理に限界を感じる
現場の作業員の安全を
遠隔からも管理したい
DXと言われても何から
手をつければいいの?
KPI(稼働率、生産性、
欠品率など)の正確な把握、
目標設定ができていない
収集した大量のデータを
活用できていない...
Ad-Sol's Solution アドソル日進なら
見える化から分析、
フィードバックまで、
トータルでサポート
豊富な無線通信の開発・導入実績を生かし、IoT やGIS(地理情報システム)、リアルタイム屋内測位システムを提案。現場調査、機器設置、データ収集から、データの見える化、分析を行い、実際の現場の課題を解決するための最適なPoC、改善施策、機器導入、システム化。さらにはデジタル人材の供給までトータルでサポートします。
Case study ソリューション事例
- CASE.1
-
車体製造ラインの見える化を行い、
作業効率の改善と品質トラブルの解決へ
お客様:自動車メーカー
お客様の課題・要望
この自動車メーカー様では、多品種の車体を組み立てる製造ラインの作業効率のさらなる改善を目指していました。また、製造工程で課題やトラブルの原因究明に時間がかかっていました。
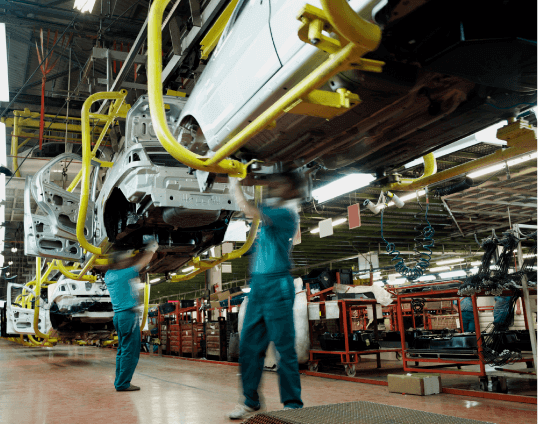
私たちの提案内容
車体製造ライン上に「高精度屋内測位 Quuppa」準拠のuLocation-Qロケータを設置。作業者がタグを所持することで"いつ""誰が"作業をしていたのかをリアルタイムで把握・記録できるように。さらに、製造ライン上に全方位カメラを取り付け、全方向の映像を録画、屋内測位システムと連動させました。
トラブルが発生した際は、誰が作業していたのかを割り出し、該当箇所の映像や画像を担当者に速やかにフィードバックする仕組みを整えました。
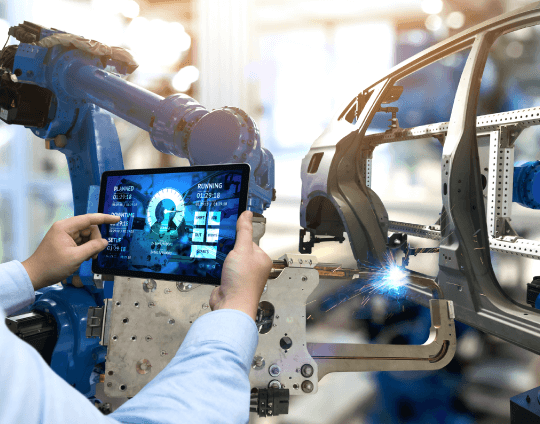
ソリューションの効果
・製造ラインでの作業が見える化され、リアルタイムに正確な工程管理が実施できるように。
・さらに詳細な状況を把握する際には、屋内測位システムで得られた作業員の動きを分析し、
要注意箇所の映像のみをピンポイントで確認。課題を速やかに見える化・特定でき、
効率的に改善活動を行えるようになりました。
・トラブルの原因究明のスピードアップを実現し、適切な防止策を講じることも可能となりました。
今後の展開
作業員の位置情報と撮影した画像に映る作業の姿勢から、作業内容を自動で判定し、各作業員のより詳細な作業時間の分析・把握を自動でできるようにしていく予定です。
- CASE.2
-
位置情報システムで置き場を管理、
ライン投入遅延を防ぎ、稼働率低下を改善
お客様:東新工業株式会社
(メッキ加工工場)
お客様の課題・要望
同社は、電子部品接点材料に部分メッキ加工を行っているが、メーカーの中間工程であるため、メーカー都合で量や品種が大きく変動し、繁忙期には入荷~出荷まで最短でも3日かかっていました。
品種も多く、保管場所も限られているため材料や完成品の定位置管理が難しく、日常的に探索業務が発生、探索コストとラインへの投入遅延の稼働率低下が大きな課題となっていました。
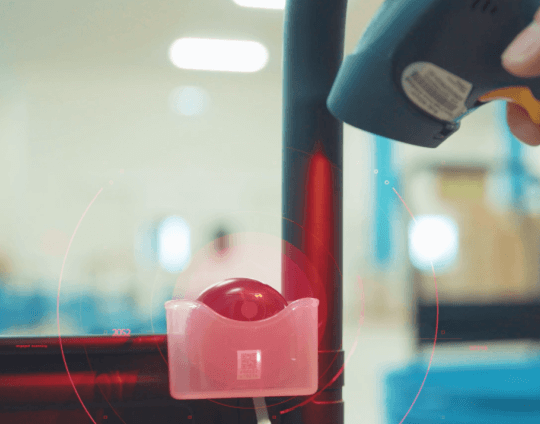
私たちの提案内容
管理エリアへの「高精度屋内測位 Quuppa」準拠システム、uLocation-Qの導入をご提案。在庫品入荷時に伝票と紐づけたタグを取り付けることで置き場における在庫品の状況をリアルタイムに把握できるようにしました。
さらに、uLocation-Qと東新工業様開発の素材位置管理ソリューションを連携させることで、作業指示書の伝票番号をタブレットアプリに入力するだけで、在庫場所をリアルタイム表示。置き場での探索を容易にする仕組みを開発しました。
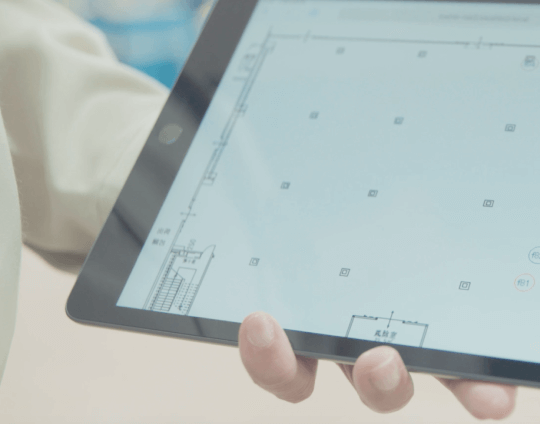
ソリューションの効果
・従来10~30分は要していた材料や在庫の探索時間を2分まで削ることができ、探索コストを削減しただけでなく、
ライン投入待ち時間の短縮により、出荷日数も短縮。製造全体でのムダを削減しました。
・同社製のアプリケーションと連動させることで、
作業員の業務負荷を増やすことなく、効率化を実現しました。
今後の展開
該当工場にとどまらず、同社の複数工場の置き場管理に展開しているほか、同社の置場管理システムと当社のuLocation-Qを連携したソリューションパッケージとして、他社への展開も検討中です。
- CASE.3
-
位置情報+カメラ+AIによる工程管理の自動化で、
車両整備の作業遅れをリアルタイムで検知
お客様:車両整備場
お客様の課題・要望
車両整備の作業進捗管理を行っていましたが、約6万平米にもおよぶ車両整備工場の敷地内での連絡手段は内線電話のみで、各現場からの連絡が滞りがち。管理者は作業状況を現場まで足を運んで確認するという非効率な状況でした。
後工程の作業員を無駄に待機させることも多く、作業遅延やトラブルの報告も遅くなり、納品遅れを招いてしまうこともありました。
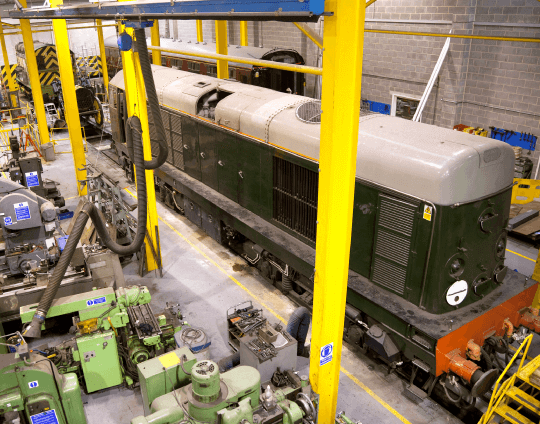
私たちの提案内容
IT化が進んでいない現場へ、クラウドを活用したシステム導入を提案。
「高精度屋内測位 Quuppa」準拠システムのuLocation-Qと車両番号自動判別AIカメラシステムを組み合わせることによって、整備車両の位置と情報を把握。工程管理を自動化しました。
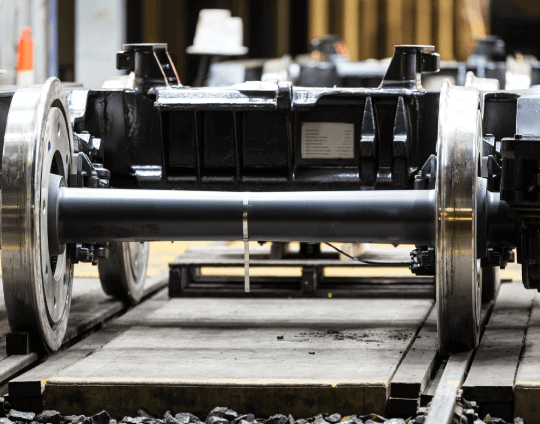
ソリューションの効果
・車体に付けられたタグによる位置情報および、カメラ映像とAIによる車両番号自動判別により、
整備車両の位置を特定し工程をリアルタイムかつ自動で管理できるようになりました。
・各作業工程の進捗や遅れをリアルタイムで検知できるようになったため、適切な作業員の配備が可能になり、
コスト削減の他、納期遅延を防ぐことができるようになりました。
今後の展開
現在は一部工程に導入している本システムを、今後、他工程への展開も検討中。
作業員にもタグを携帯してもらうことで、誰が、いつ、その作業をしているかといったより詳細な工程の管理も視野に入れています。
- CASE.4
-
小ロット多品種製造ラインを見える化、ライン毎の工数の
自動収集で正確な製造原価を把握し、残業抑制・工程見直しを実現
お客様:キャビネットメーカー
お客様の課題・要望
小ロット多品種製造ラインにおける個々の製造工数をストップウォッチで手動計測していたため、正確な工程管理・原価把握ができていませんでした。
進捗チェックが日に2回にもおよんでいたほか、適切な業務改善ができず、残業の原因となっていました。
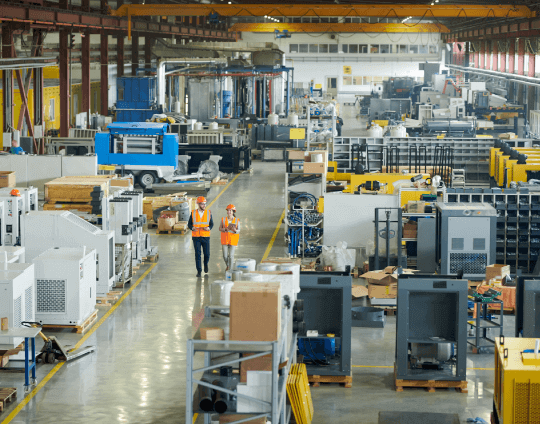
私たちの提案内容
小ロット多品種製造ラインの製造工程に、「高精度屋内測位 Quuppa」準拠システムのuLocation-Qを導入をご提案。
製造ラインごとにuLocation-Qロケータを設置することで、ライン毎の作業員の位置を検知。作業の着手・完了を正確かつ自動で把握できるようにしました。
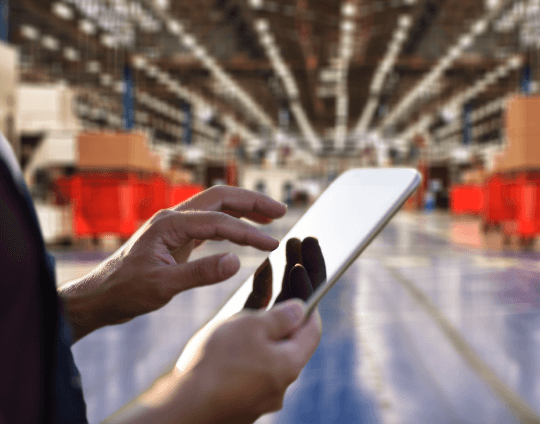
ソリューションの効果
・屋内測位システムと工程管理アプリケーションを連携させることにより、
各工程の正確な着手と完了を人手に頼らず自動収集できるようになり、正確な製造原価の把握が可能に。
・予実績のリアルタイム管理も可能となり、残業抑制を実現しました。
今後の展開
今後は、収集したデータをAIで分析、ボトルネックを事前予測し、製造工程のKPIと関連付けることにより、さらなる業務改善を行う予定です。
Related Sites 関連サイト
高精度屋内測位
uLocation-Q
SUNMAP